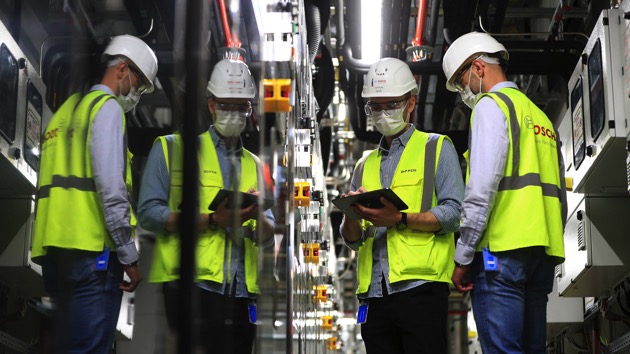
(NEW YORK) — In an increasingly digitized world, almost no industry has been left unscathed by the global shortage of electronic chips.
Demand for these dime-sized building blocks needed to make cars, computers, smartphones and much more was growing even before reaching a fever pitch as the COVID-19 pandemic forced swaths of the globe to rely on tech tools for work or school. The shortage also clobbered the auto industry with disproportionate furor, leading to skyrocketing new and used vehicle prices — which in turn drove one-third of all of the painful inflation Americans saw in 2021, according to the Bureau of Labor Statistics.
The crisis has exposed just how bedeviling the pandemic has been for policymakers and business leaders who failed to foresee the fallout from this shortage coming, as well as exposed the risks for U.S. business that results from a majority of the world’s chip supply being produced in Asia — and more specifically, political tripwire-ridden Taiwan.
“It is both an economic and national security imperative to solve this crisis,” Secretary of Commerce Gina M. Raimondo said in a blogpost Tuesday, sharing fresh data on the fragility of the semiconductor supply chain and calling on Congress to approve $52 billion in chips funding “as soon as possible.”
As the scarcity of semiconductors continues to dominate headlines two years into the pandemic, here is what economists say Americans should know about the chip shortage, and what its implications are for the future.
‘An essential part of almost every product that we use’: What are semiconductors?
“Semiconductors, or chips as we call them, are sort of the building blocks of any computer system,” Morris Cohen, an emeritus professor of Manufacturing and Logistics in the Operations, Information and Decisions Department, at the University of Pennsylvania’s Wharton School, told ABC News.
“There’s been incredible advancements over the years in the capabilities of these chips, in reduction of their size and power requirements,” Cohen added. “And so we see them now embedded everywhere — in your cellphone and your computer, in your home appliances, and in your automobile.”
“These devices are used to monitor performance to control function, to capture data to send instructions and so on,” Cohen added. “They’ve become sort of an essential part of almost every product that we use.”
Awi Federgruen, a professor of management at Columbia Business School, told ABC News that the chip shortage “is being felt in no less than 169 industries.”
As the tech sector continues to expand at a rapid pace and a growing array of tools and gadgets become embedded in Americans’ daily life, an increasing number of products are becoming dependent on chips. The implications of this can be felt by consumers shopping for everything from portable gaming systems to smart kitchen appliances, and many have likely already noticed higher prices or longer wait times when searching for their products.
Meanwhile, a reliance on chips for critical medical devices, military applications, cybersecurity tools and other sectors can carry more serious ramifications for both individuals and governments.
One natural disaster away from hitting American jobs: How severe is the shortage?
The median inventory held by chip consumers (such as automakers or medical device manufacturers) has sunk from a 40-day supply in 2019 to a less than five-day supply in 2021, the Commerce Department said in an industry report released Tuesday.
This means that if a natural disaster, COVID-19 outbreak or political instability disrupts a semiconductor facility abroad for even just a few weeks, it has the potential to shut down a manufacturing facility in the U.S., the agency added, putting American workers at risk.
Moreover, median demand for chips from buyers was as much as 17% higher in 2021 than in 2019, according to the report, and the majority of semiconductor manufacturing facilities are operating at or above 90% utilization — meaning there is limited additional supply to bring online without the expensive and time-consuming process of building new facilities.
The majority of chip factories are currently based in Asia, which houses about 87% of the market share of semiconductor factories (with Taiwan alone accounting for some 63%), separate industry data indicates. The political climate in the region, and tensions between Taiwan and China, has come under renewed scrutiny as the shortage has exposed how much U.S. industry relies on these sources.
“Initially, when you go back to the origins of the industry, the majority of the capacity was in the U.S. and then it shifted outside,” Cohen told ABC News. “Now, there’s a big push to re-shore that manufacturing and bring it back, and it’s not just a business decision, it’s political, it’s a highly politicized decision.”
‘A perfect storm’: What is causing the shortage?
The supply-demand imbalances in the semiconductor industry were already fragile before the pandemic, and the Commerce Department noted in its report that underlying demand for semiconductors was already growing prior to 2020, propelled by industry shifts such as the onset of 5G and electric vehicles. The pandemic then exacerbated the crisis by causing a surge in demand for products that require semiconductors while simultaneously disrupting the supply.
Columbia’s Federgruen said the current shortage is the result of multiple factors creating “a perfect storm.”
Silicon, the raw material used in chips, became harder to come by for producers during the pandemic, according to Federgruen, because it is necessary for vaccine manufacturing.
“In addition, there was the shutdown or temporary shutdown of [semiconductor] manufacturing facilities in the Far East and elsewhere, as a direct result of the of the pandemic,” Federgruen said. “And then there is the fact that on the demand side, in many industries such as the automobile industry, there’s been an unusual ramp-up of the demand.”
“All those factors have come together and compounded upon each other to create a big, big shortage,” Federgruen said.
Why is it hitting the auto industry so hard?
Most Americans by now have heard of the shortage’s impacts on the auto industry, which has been among the most severely hit by the shortage as more cars today are being fuzed with additional electronic systems than in the past, Federgruen told ABC News.
The shortage was compounded in the auto industry because many carmakers initially thought the pandemic would crush demand and planned for this by reducing semiconductor orders. An apparent desire to avoid public transportation and plan getaways closer to home during the health crisis, however, ended up having the opposite effect on demand for autos. Chip manufacturers, already suffering from pandemic-related shocks, could not keep up with the new orders coming in from the auto industry that came as a simultaneous remote-work boom spurred demand for chips needed for computers and IT tools.
Raimondo said that the so-called legacy logic chips used in automobiles — as well as medical devices — are facing the most acute shortages.
“In 2021, auto prices drove one-third of all inflation, primarily because we don’t have enough chips,” Raimando wrote in her blogpost. “Automakers produced nearly 8 million fewer cars last year than expected, which some analysts believe resulted in more than $210 billion in lost revenue.”
Cohen, from the Wharton School, added that over the last decade or so, “the amount of computer systems that are put into a car has just increased enormously.” While carmakers have become big users of chips for managing vehicles’ entertainment, climate, fuel systems and more, they have continued to rely on outsourced production and suppliers for these parts.
Automakers historically did not consider producing chips to be their core competency, but many have come to the realization now that they can’t afford to be dependent on outside suppliers for chips if their absence can bring production and assembly lines to a screeching halt.
Raimondo called new partnerships with semiconductor producers recently announced by Ford and General Motors “encouraging” in her blogpost Tuesday, saying the announcements “demonstrate that chip consumers and producers are coming together to solve their supply chain issues.”
What is being done to address the shortage, and how long will it last?
The Commerce Department’s report said that industry players do not see the significant, persistent mismatch in the supply and demand for chips going away in the next six months.
The report identified the main issue as the need for additional semiconductor factories (also called semiconductor fabrication plants or fabs). Construction of new fabs, however, is expensive and can take years before making an impact in the supply.
In addition to the steps taken by players in the auto industry such as Ford and GM, some companies have also announced new and dramatic actions to ameliorate the crisis and bring semiconductor manufacturing back to the U.S.
Intel announced late last week that it was investing more than $20 billion to build two new chip factories in Ohio — a headline-grabbing announcement that came on the heels of the firm saying last October that it had began construction on two chip factories in Arizona. Samsung similarly announced plans late last year to build a $17 billion semiconductor factory near Austin, Texas.
“It’s great that they’re doing that but it’s not going to solve today’s problems, that’s for sure,” Cohen told ABC News of the recent announcements. “It’ll take years for this to take place, and in the interim, we’re still going to have to source these products from the places they come from now. We don’t have an alternative.”
The situation may improve slightly if demand cools off, Federgruen noted, but similarly said that it will take years for the “big change” to occur when these new U.S. facilities begin actually pumping out chips.
Why should Americans care and what does this mean looking ahead?
Cohen said that having studied the industry for a long time, a lot of what we’re seeing now could have been anticipated to some degree, especially among industry players.
“Companies who operate in this environment have been aware of these issues for a long time and have dealt with it,” he said. “This is just the nature of being competitive in those industries.”
If a new fab costs billions of dollars and takes years to construct, companies in an increasingly globalized world will likely turn to offshore suppliers for chips instead. Cohen said the pandemic, however, has made Americans more aware of risks and fragility of this dependence on outside suppliers.
“Most consumers didn’t know and didn’t care where their chips came from: ‘You turn the car on, it should go, I don’t really care who made the chip and what country it was built in,'” Cohen said. “But now, all of a sudden, these issues become really important, and so I think we become more sensitized to how dependent we are, how interdependent we are, how things can be disrupted.”
“We became a globalized economy because there were a lot of advantages,” Cohen added. “Because of that, we as consumers have enjoyed access to an amazing array of products and incredibly low prices, which has increased our standard of living.”
With chip supply now just one natural disaster or major disruption away from potentially impacting American livelihoods, Cohen predicts it is “going to be difficult to maintain the status quo.”
“We will have more expensive products, we’ll have things that will take longer,” he said. “Therefore, our standard of living to some extent will be lower. It’ll cost us more time and money to earn what it takes to buy a car, to buy a house.”
Federgruen added that he hopes policymakers and business leaders can learn from the lessons exposed by the crisis and make better decisions moving forward that don’t just take into account short-term profits.
“In general, there’s been the recognition that we need to make our supply chains much more resilient, and that we need to build in safety buffers on the supply side for situations like this,” Federgruen told ABC News. “That lesson comes up with every crisis and is then forgotten, unfortunately, but hopefully it will stick now.”
Copyright © 2022, ABC Audio. All rights reserved.